

As discussed, distribution of electric field inside such a construction, is highly non-uniform in terms of both axial and radial components. The basic principle in bushing design consists of a conductor surrounded by an insulating solid cylinder that is mechanically fixed to the earthed barrier. The benefits of narrower external diameter translate into lower cost for the housing, reduced weight, less oil and less clearance diameter of the embedded shielding in the lower part. But to handle the same stress, an identical ungraded bushing would need a housing of almost double that diameter. For example, the porcelain housing diameter on a simple 110 kV field-graded bushing is about 240 mm measured across the sheds. On fine-graded bushings, stress is linearized and spread over more distance, resulting in greater safety margin. On ungraded bushings, electric field tends to be concentrated around the flanges and therefore risk of breakdown becomes high. One of the motivations behind development of field-graded bushings was reducing the diameters required for the porcelain housings. These were later modified to designs involving less conductive grades of paper along with aluminum foil. Originally, materials used in the cylinders wound around the conductor included resin-bonded paper and carbon materials. The basic principle was to distribute the natural field between conductor and earthed flange by employing intermediate conductive layers radially (to lower the field at the conductor and better utilize the insulation material) and also axially (to allow for higher flashover voltage values for a given arcing distance). This resulted in designs that were capacitance-graded.
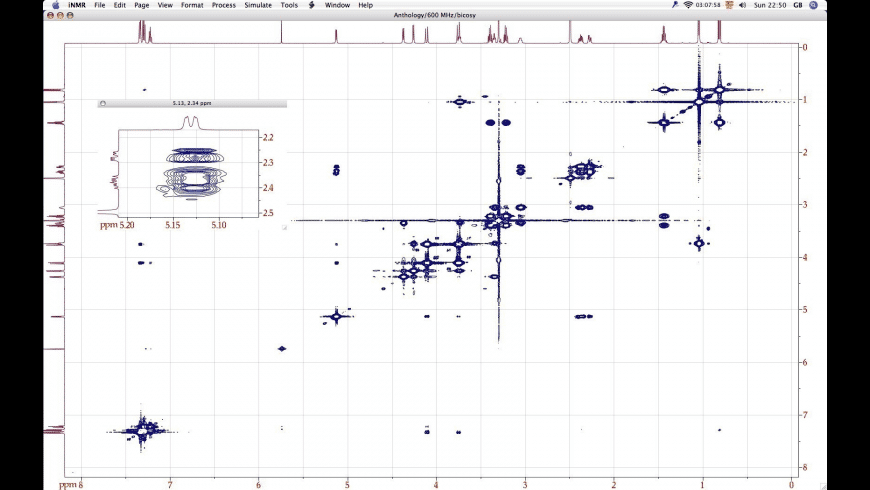
But as networks have become more sophisticated, the need was recognized to better distribute the electric field generated across a bushing – especially at higher voltages. Such simple bulk and solid type bushings are in fact still being applied at medium voltage levels. In their early years, bushings were little more than hollow porcelains filled with transformer oil or solid resin surrounding the conductor. Catastrophic bushing failure means expensive repairs or even total loss of transformer. Explosion of this OIP bushing in New Zealand launched porcelain shrapnel over wide adjoining residential area (dotted blue boundary). Certain types of bushings can threaten not only substation personnel but even nearby communities. While bushings account for only about 5% of the cost of a power transformer, their catastrophic failure can lead to total loss of the transformer and possibly other expensive equipment as well. Like a surge arrester, a bushing is a relatively low cost component ensuring the safe operation of a high value asset. Stanislaw Gubanski of Chalmers University of Technology in Sweden with excerpts from issues of INMR. This edited overview combines an edited contribution to INMR by retired Prof. Moreover, a bushing must have the proper thermal design to avoid overheating of any of its components and prevent onset of ageing phenomena in its insulation – both at rated current and during short circuit events. Another key requirement is providing the mechanical strength needed to support the conductor as well as all external connections, including under short circuit and possible seismic forces. For example, bushings must provide reliable electrical insulation both internally (against breakdown) and externally (against flashover) of the conductor exposed to the rated voltage and also to periodic service overvoltages – even under contaminated conditions. An integral part of this function involves meeting all the electrical, thermal and mechanical requirements of the application. Bushings are devices that allow conductors to pass through the earthed walls of transformers, switchgear and substation structures.
